In today’s market brands wrestle with inconsistent frame quality and shipment delays that erode customer trust. This guide solves those pain points by walking through each stage of sunglasses production from material choice through compliance checks. We draw on ten years of supplying leading eyewear labels so you gain actionable tips that cut risk and speed time to market. Ready for the good part? Follow our proven framework and you will streamline batches reduce defects and uphold your brand’s reputation in a crowded field.
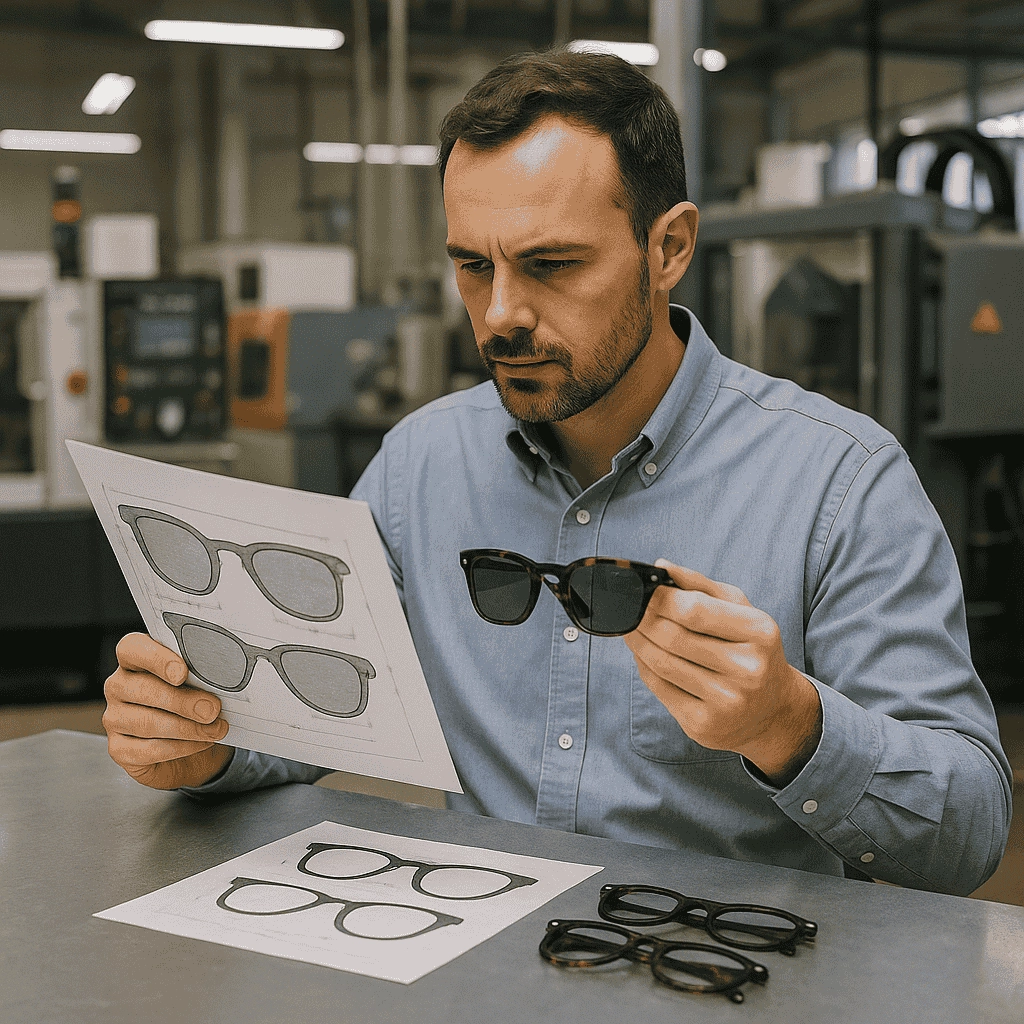
1 What Materials Are Used In Sunglasses Manufacturing?
Brands must pick components that balance style durability and budget. But here’s the kicker… material choice sets the stage for every subsequent process. Acetate offers rich color depth and structural stability yet demands longer mold cure times. Stainless steel presents sleek lines and corrosion resistance though it feels heavier on the face. Titanium delivers unmatched strength at minimal weight but carries premium cost that impacts unit price. When planning a run weigh each option against target audience expectations and price positioning before tooling begins.
Lens selection drives performance wearer comfort and legal compliance. Polarized lenses cut glare on water or roads enhancing clarity for outdoor use. Gradient tints tap fashion trends without sacrificing UV filtering performance required under CE or FDA protocols. Fully mirrored coatings complement bold designs though they can increase scratch risk if overused. Durability testing under heat and abrasion conditions reveals which lens treatments endure regular wear in diverse climates.
Hardware and hinges also matter. Spring hinges enable temple flex that reduces frame stress and extends life span by up to 30 percent according to field studies. Barrel hinges cost less but offer limited adjustability that can lead to customer complaints when fit varies. Selecting corrosion-proof screws matched to frame thickness prevents cracks during assembly. What’s the real story? overlooking small parts often triggers bulk returns and warranty claims that undermine margins.
By aligning frame lens and hardware decisions you build a sturdy foundation for mass production. Invest in small-batch trials to validate color fidelity and fit tolerances. Early component testing cuts sample cycles and reveals latent defects long before full-scale tooling.
Material Component | Key Benefits | Manufacturing Considerations |
---|---|---|
Acetate Frame | Vibrant hues stable form | Longer cycle times higher mold cost |
Stainless Steel | Sleek profile high corrosion resistance | Heavier feel limited color choice |
Titanium Frame | Lightweight hypoallergenic strong | Premium pricing requires niche positioning |
Polarized Lens | Glare reduction enhanced clarity | Higher cost complex assembly |
Spring Hinge | Flexible fit fewer breakages | Slightly higher hardware expense |
2 How Do Designers Create A Sunglasses Concept?
Early product development can stall when teams chase trends without manufacturing insight. This is where it gets interesting… successful concepts spring from rigorous market research paired with hands-on feasibility checks. Designers start by compiling trend data from fashion runways social platforms and consumer surveys. They pin down shapes color palettes and lens styles that resonate with target segments before sketching dozens of silhouette variations. Hand-rendered sketches foster creativity and rapid iteration during brainstorming sessions.
Once initial sketches earn stakeholder buy-in they move into digital mockup using CAD tools. These digital prototypes capture precise dimensions temple curvature and lens pocket geometry. That clarity prevents miscommunication between design and production engineers who must confirm material bend limits and hinge integration points. Early cross-functional reviews slash sample rounds by two iterations on average according to factory reports.
Ready for the good part? virtual sampling via 3D rendering lets teams spot misalignments color mismatches and balance issues without costly physical prototypes. Designers overlay brand logos on mockups to ensure legibility at different scales and test temple engraving options in multiple finishes. Packaging concepts often evolve simultaneously so unboxing delights align with frame aesthetics from the first glance.
By shadowing each concept through trend analysis digital modeling and virtual sampling brands unlock faster development schedules and tighter cost controls. Early collaboration between marketing design and production teams prevents late-stage redesigns that inflate budgets and push back launch dates.
Concept Phase | Tools Used | Key Outputs |
---|---|---|
Trend Analysis | Fashion reports social media | Clear style directives |
Sketch Ideation | Pencil paper | Multiple silhouette options |
CAD Mockup | 3D modeling tools | Precise dimensional blueprints |
Virtual Sampling | Rendering software | Color and balance validation |
Engineering Review | Cross-functional workshops | Feasibility confirmation |
3 How Is A Prototype Made?
Moving from concept to prototype tests real-world fit form and function before full-scale investment. But here’s the kicker… skipping a robust prototype can trigger costly tool redesigns and production delays. Prototyping begins with cutting raw blank material—acetate sheets or metal strips—into rough frame shapes via laser or manual trimming. Those blanks then enter CNC machines for lens pocket carving and hinge barrel drilling maintaining 0.1 millimeter tolerances crucial for smooth assembly.
Next comes hand finishing where technicians smooth rough edges polish acetate surfaces and remove laser burn marks. Spring hinges install at this stage allowing fit checks under varied temple tension. Preliminary lenses cut by radius machines slot into frame pockets for visual trials that reveal lens-edge alignment issues. What’s the real story? wear-test sessions expose comfort hotspots that CAD simulations cannot anticipate such as temple pinch or frame weight distribution concerns.
Prototypes often travel through rapid iteration loops. Feedback from in-house stylists QA engineers and select customer panels feeds into design tweaks. Each cycle adds polish and refines component interplay. By limiting prototype batches to 5–10 units brands keep costs in check while validating critical dimensions and aesthetic decisions.
Final prototype approval paves the way for mold manufacturing or stamping die orders. That green light ensures tooling begins on stable design saving weeks of back-and-forth. Investing time in thorough prototyping reduces scrap rates during mass production and heightens customer satisfaction at launch.
Prototyping Stage | Process | Outcome |
---|---|---|
Blank Cutting | Laser/Manual | Rough frame silhouette |
CNC Machining | Automated carving/drilling | Precise dimension adherence |
Hand Finishing | Sanding polishing | Smooth surface premium look |
Lens Fitting | Radius cutting insertion | Visual and fit validation |
Wear Testing | Internal/external feedback | Ergonomic and aesthetic refinement |
4 What Tooling Is Needed For Full-Scale Production?
Scaling from prototype to production demands specialized tooling that withstands high cycle counts. This is where it gets interesting… injection molds carve acetate frames under heat and pressure delivering consistent wall thickness and shape fidelity. Those molds often cost tens of thousands yet spread cost over thousands of units driving per-piece price downward. Metal frame production relies on stamping dies that shear shape hinge barrels temple strips and bridge profiles from sheet steel or titanium. Die longevity hinges on material hardness and precise die steel grades selected during design.
Beyond primary shaping tools secondary jigs and fixtures optimize downstream processes. Polishing fixtures hold frames steady under abrasive belts ensuring uniform surface finish. Ultrasonic welding machines cuff temple tips or attach nose pad brackets with precise energy delivery that avoids overheating. Drilling jigs lock frames in defined positions so hinge holes and decorative cutouts align across every unit. But here’s the kicker… investing in modular fixturing allows rapid changeovers between models slashing downtime when production switches.
Tool maintenance protocols also weigh heavily on yield rates. Scheduled die polishing and mold cavity cleaning ward off defects like flash lines or incomplete fills that degrade aesthetics. Calibration of CNC cutters and drill bits ensures hole tolerances remain within ±0.05 millimeters preserving hinge fit across batches. Without rigorous tooling upkeep run rejects can spike from under 1 percent to over 5 percent within weeks.
By designing robust tooling systems and maintenance schedules brands secure consistent output quality and predictable lead times essential for B2B reliability.
Tooling Category | Purpose | Maintenance Needs |
---|---|---|
Injection Molds | Acetate frame shaping | Cavity cleaning periodic polishing |
Stamping Dies | Metal frame forming | Die steel inspection edge regrinding |
Polishing Fixtures | Surface finishing | Abrasive belt replacement cleaning |
Ultrasonic Welders | Brace attachment nose pad fitting | Transducer calibration energy checks |
Drilling Jigs | Hole alignment for hinges and hardware | Alignment validation every shift |
5 How Does Lens Cutting And Finishing Work?
Lens cutting transitions raw lens blanks into precise optical components ready for assembly. Ready for the good part? the process begins with selecting correct blank curvature and material thickness based on Rx requirements or fashion lens styles. CNC radius machines carve lens edges matching frame pocket profiles with ±0.02-millimeter accuracy essential for secure fit. High-speed diamond-tipped tools abrade glass or polycarbonate surfaces to shape before moving into beveling stations that smooth edges and create precise 90-degree or custom bevel angles.
Next lens finishing applies coatings that guard against scratches glare and UV radiation. Anti-scratch layers deposit via vacuum sputtering creating microscopic metal oxide bonds that strengthen surface resilience. Polarizing films sandwich between lens substrates in multi-step lamination cycles that require controlled temperature and pressure to avoid delamination. Finally hydrophobic and oleophobic coatings resist water oil and fingerprint adhesion improving wearer comfort and lens longevity. What’s the real story? skipping final quality checks on coating thickness or uniformity can yield lenses that fail compliance tests under ISO-12312 standards risking product recalls.
Automated inspection stations scan lens surfaces under bright-field lighting capturing high-resolution images that pinpoint defects as small as 5 microns. Spatial uniformity checks confirm coating consistency across the entire lens area. Shape verification scanners measure edge profiles against CAD data flagging any deviations beyond acceptable tolerance bands.
By combining precise cutting with advanced finishing and stringent inspections brands produce lenses that fit elegantly enhance vision and comply with global safety regulations delivering wearer satisfaction and brand credibility.
Lens Process Stage | Equipment Used | Quality Control Metric |
---|---|---|
CNC Edge Cutting | Radius cutters | ±0.02 mm dimensional accuracy |
Beveling | High-speed bevelers | Edge angle consistency |
Coating Application | Vacuum sputtering systems | Coating thickness uniformity |
Lamination | Temperature-controlled presses | Delamination absence |
Surface Inspection | Automated vision scanners | Defect detection down to 5 microns |
6 How Are Frames Formed And Assembled?
Frame construction demands precision heat control and skilled labor to translate raw components into finished sunglasses ready for finishing touches. But here’s the kicker… the assembly phase determines final fit comfort and structural integrity far more than initial cutting or tooling. Acetate frames journey from blank to shape in heated water tanks set to precisely 90 °C. Technicians submerge acetate arms and fronts until material pliability peaks then place pieces into CNC-cut metal molds. Those molds clamp shut applying even pressure to ensure curvature consistency across both sides. After cooling in controlled environments technicians remove frames and inspect each for warp or asymmetry under LED-backlit inspection tables.
Metal frames follow a different route. Stainless steel or titanium strips feed into automated bending machines programmed with exact radii for bridge arches and temple curves. Each bend requires calibrated rollers and pressure gauges to avoid microfractures that compromise fatigue resistance. Once basic shape forms workers solder or laser-weld hinge barrels and nose pad mounts using inert gas shields that prevent oxidation at weld sites. This is where it gets interesting… ultrasonic welding can also fuse temple tips or attach decorative inlays without visible seams offering a cleaner aesthetic favored in premium lines.
Hinge installation demands meticulous alignment. Spring hinges slide into pre-drilled barrels then technicians apply torque wrenches set to 4 N·m to secure screws without stripping threads. Frames travel on conveyor belts through torque-check sensors that reject units if torque exceeds or falls below tolerance ranges. Next stations use infrared cameras to verify temple symmetry and frame balance by capturing side-angle profiles and overlaying them onto CAD templates. Those that pass move on to buffing arms where soft brushes and microfiber pads remove any micro-abrasions left by form-holding fixtures.
By mastering these forming and assembly techniques brands cement quality at scale. Early investments in precision molds CNC fixtures and automated quality checks yield fewer rejects lower long-term costs and consistent consumer satisfaction.
Assembly Stage | Key Actions | Quality Check |
---|---|---|
Acetate Heating & Molding | Submerge at 90 °C mold clamp for curvature | LED inspection for warp under backlit table |
Metal Bending | Rollers bend to programmed radii | Stress testing for microfracture detection |
Hinge Welding/Soldering | Laser or ultrasonic weld hinge barrels | Visual weld seam inspection |
Screw Torque Calibration | Apply 4 N·m torque on spring hinges | Conveyor torque sensors reject out-of-range units |
Buffing & Polishing | Soft brush microfiber pad finish | Surface sheen consistency check |
7 How Is Lens Insertion Handled?
Lens insertion bridges the gap between frame construction and final eyewear assembly requiring finesse to avoid stress cracks or misalignment. Ready for the good part? precise lens fitting elevates both aesthetics and lens performance in daily use. For full-rim frames technicians align lens edges with corresponding frame pockets, then apply a thin layer of UV-cure adhesive around the perimeter. Automated dispensing heads deposit exactly 0.05 ml per lens quadrant reducing excess material that could overflow during curing. Workers then position lenses and expose assemblies to 365 nm UV light for 30 seconds ensuring complete polymer cross-linking. That rapid curing process prevents lens movement during shipping or wear.
Rimless and semi-rimless designs demand mechanical retention methods. Drill-and-nut systems treat lenses with protective gaskets before using CNC drills to bore 1 mm holes at precise coordinates. Stainless steel nuts and screws fasten through lens holes into frame temples or bridge components tightening to 0.8 N·m torque using digital torque drivers. What’s the real story? adding silicone gaskets between lens and hardware cushions stress concentrations that often cause cracks especially in polycarbonate optics under cold conditions.
Safety checks on inserted lenses involve pressure testing chambers that simulate up to 8 kg force applied at temple tips. Assemblies that show any lens displacement or gasket failure get flagged for rework. Optical alignment stations next project cross-hair patterns through lenses onto wall screens verifying that optical centers match design specifications within ±0.5 mm. That step ensures wearers won’t experience prismatic distortion or eye strain over extended periods.
By combining automated adhesive dispensing mechanical retention systems and rigorous inspection protocols brands achieve durable lens-frame integration that stands up to real-world challenges.
Insertion Method | Technique | Inspection Criteria |
---|---|---|
UV-Cure Adhesive | Automated dispense align UV light cure | No adhesive overflow bond strength test |
Drill-And-Nut System | CNC drill holes add silicone gaskets screw | Torque check lens displacement under 8 kg force |
Optical Center Alignment | Project cross-hair pattern through lens | ≤ 0.5 mm deviation from CAD optical center |
Temperature Cycling | Simulate −20 °C to 60 °C lens expansion test | No visible lens cracks or distortion |
Visual Surface Check | LED-lit inspection for air bubbles or voids | Zero voids larger than 0.1 mm diameter |
8 How Is Quality Control Performed?
Effective quality control weaves through every production stage catching defects early decreasing waste and bolstering brand trust. But here’s the kicker… setting up QC gates properly saves time and expense compared with end-of-line scrapping. Incoming material inspections begin with sampling 5 percent of acetate sheets or metal strips. Technicians measure sheet thickness color consistency and tensile strength against vendor certificates using micrometers spectrophotometers and tensile analyzers. Failing lots get quarantined preventing substandard stock from entering production.
Inline process checks accompany molding and bending operations. Injection mold cavities undergo cavity and core measurement scans daily verifying tolerances within ±0.1 mm. CNC cutters get tool length measured after 500 cycles to adjust for wear. Laser weld setting logs record power output and duration for each weld cycle ensuring consistent joint penetration. This is where it gets interesting… automated vision systems capture 4 K images of frame edges and hinges detecting burrs or mis-alignments invisible to the naked eye.
Post-assembly QC happens on rotating tables under multi-angle lighting where trained inspectors examine reflective surfaces for scratches coating defects or logo misprints. Random pull tests apply 3 kg force to temple tips measuring hinge resilience. Lenses receive scratch-resistance tests using calibrated abrasers that run 200 cycles under 0.75 N load determining coating adhesion performance. Optical clarity assessments project test charts through lenses recording contrast and light transmission percentages against ISO-12312 benchmarks.
Final batch audits involve statistical process control charts plotting defect rates cycle times and yield trends. Ready for the good part? interpreting SPC data highlights process shifts before problems balloon into large-scale rejects saving up to 15 percent in rework costs. Comprehensive QC protocols give B2B buyers confidence knowing every order meets agreed standards.
QC Stage | Method | Acceptance Criteria |
---|---|---|
Material Inspection | Micrometer spectrophotometer tensile test | Vendor spec compliance 100 percent |
Inline Mold Verification | CNC scan tool length daily | ±0.1 mm cavity tolerance |
Automated Vision Check | 4 K image capture edge and hinge check | Zero burrs or misalignment > 0.05 mm |
Pull Test | 3 kg temple tip force | No hinge failure |
Optical Clarity Test | Chart projection light transmission | ≥ 90 percent compared with ISO-12312 standards |
9 What Regulatory Standards Apply?
Navigating international eyewear regulations ensures products clear customs and satisfy end-user safety requirements. What’s the real story? missing a CE or FDA mark can block shipments and trigger costly recalls undermining market reputation. In Europe Sunglasses must comply with EN ISO 12312-1 specifying UV protection lens transmittance limits frame impact resistance and labeling guidelines. That standard demands lenses block at least 99 percent of UV-B rays and maintain visible light transmittance between 8 percent and 80 percent depending on category. Impact tests drop a 22 mm steel ball from 1.27 m measuring shatter resistance under direct and lateral conditions.
US FDA regulations treat sunglasses as medical devices requiring 21 CFR 801 labeling that covers manufacturer identification and warnings against unapproved medical claims. FDA also enforces ANSI Z80.3 standards for non-prescription sunglasses specifying optical power tolerances and lens defect limits. Sunglasses entering the UK market need UKCA marking under the UK Conformity Assessed regime mirroring EU rules post-Brexit yet requiring separate registration processes. But here’s the kicker… even subtle differences in labeling format or language translations can delay customs clearance up to two weeks in key markets like Germany or France.
Packaging inserts and hang tags must list frame material, lens category, UV protection level and model identification codes. Barcode inclusion aligned with GS1 standards speeds warehouse scanning operations reducing order-pick errors. Documentation dossiers for each SKU contain test reports calibration certificates and production batch records ready for buyer audits or regulatory spot checks.
By mastering these standards and embedding compliance checks at prototyping and production stages you avoid red-tape delays and build buyer trust critical for B2B partnerships.
Region | Standard | Key Requirements |
---|---|---|
Europe (EU) | EN ISO 12312-1 | UV-B ≥ 99 percent impact resistance labeling details |
United States | FDA 21 CFR 801 ANSI Z80.3 | Manufacturer ID optical tolerance defect limits |
United Kingdom | UKCA | Mirror EU specs separate registration |
Global Trade | GS1 barcode | Barcode on packaging scan accuracy |
Documentation | Test reports dossiers | Batch records calibration certificates compliance logs |
10 How Do You Select A Reliable Supplier?
Choosing an eyewear supplier blends due diligence site visits and sample evaluations to pinpoint partners aligned with brand quality and capacity needs. Ready for the good part? begin by verifying certifications—CE FDA UKCA ISO 9001 or ISO 13485 audits provide insight into factory quality systems and production controls. Review audit reports focusing on process documentation, corrective action history and supplier performance metrics over the past year.
Next arrange factory tours either in-person or virtual using high-definition live streams. Observe production floors for equipment types mold maintenance zones and material storage conditions. Ask detailed questions about mold changeover times average yield rates and staff training programs. Pay special attention to how factories manage non-conformance incidents and implement continuous improvement loops. But here’s the kicker… seeing a spotless showpiece production line on arrival may mask off-site subcontracting practices that erode quality consistency. Insist on viewing actual molding and assembly cells where your SKUs will run.
Sample ordering forms the final validation step. Request 10–20 pairs across multiple colorways and sizes. Track lead times from order confirmation through delivery and document defect rates and packaging accuracy. Conduct independent lab tests on lens UV ratings frame tensile strength and coating adhesion verifying internal QC claims. Negotiate clear terms for rework allowances defective unit thresholds and warranty obligations documented in purchase agreements.
By combining certification reviews live factory audits and comprehensive sample testing you establish supplier relationships built on transparency accountability and mutual quality goals.
Selection Step | Action | Success Metric |
---|---|---|
Certification Review | Audit CE FDA UKCA ISO reports | Zero critical non-conformances |
Factory Audit | In-person or virtual floor inspection | Verified equipment and process adherence |
Sample Testing | Order 10–20 pairs lab evaluation | Defect rate ≤ 2 percent |
Lead-Time Tracking | Document order confirmation to delivery | On-time delivery ≥ 95 percent |
Contractual Terms | Define rework warranty thresholds | Clear SLA with penalty clauses |
11 How Is Cost Estimated For A Production Run?
Cost estimation hinges on raw material pricing labor overhead and tooling amortization that directly impacts unit economics and profit margins. But here’s the kicker… failing to account for hidden costs like mold maintenance or quality rework inflates expenses unexpectedly. Begin by calculating material spend based on frame substrate weight lens surface area and hardware counts per unit. Acetate sheets often quote per kilogram rates while metal strip pricing ties to material grade and thickness. Add lens blank costs differentiated by functions such as polarization or anti-scratch coatings.
Labor cost divides into direct assembly hours and indirect tasks like inspection packaging and logistics coordination. Time-motion studies reveal average cycle times per frame and lens insertion enabling precise hourly labor allocations. Overhead includes facility utilities equipment depreciation and management salaries apportioned across production volume. Tooling amortization spreads initial mold or die investment over projected unit counts. For example a $20 000 acetate mold run for 10 000 units adds $2 per frame upfront. This is where it gets interesting… adjusting amortization based on actual output rather than forecasted volume prevents under-recovering costs when orders fall short.
Packaging and shipping add further layers. Customized cases pouches and instruction inserts require design and printing costs while bulk shipping quotes vary by weight volume and destination. Factor warehousing fees for storage between production and distribution. Ready for the good part? negotiating tiered pricing with logistics partners based on minimum monthly volume can cut freight rates by up to 15 percent according to industry insiders.
Summing these components then adding target markup yields per-unit pricing for client quotations. Regular review of cost drivers ensures competitive pricing without sacrificing margin. Accurate cost estimation fosters transparent client conversations and prevents margin erosion over long-term partnerships.
Cost Component | Calculation Basis | Example Cost Impact |
---|---|---|
Material | Frame weight lens area hardware count | $3.50 per acetate frame $2 per lens |
Labor & Overhead | Cycle time hourly rate overhead apportion | $1.20 assembly $0.50 inspection |
Tooling Amortization | Mold cost spread over forecast units | $2 per frame for 10 000 unit mold |
Packaging | Case pouch insert design print | $0.80 per unit |
Shipping & Logistics | Weight volume destination negotiated rate | $1.10 domestic $2.40 international |
12 What Packaging Options Exist For Bulk Orders?
Packaging transcends mere protection offering brand differentiation and regulatory compliance all while containing costs that affect final bid competitiveness. But here’s the kicker… selecting wrong materials or designs can trigger damage claims or excess freight fees due to oversize dimensions. Begin by exploring hard cases crafted from durable ABS or metal-reinforced shells providing premium perceived value. Soft pouches made of microfibre or neoprene reduce weight and shipping volume yet deliver basic scratch protection. Consider dual-pack boxes that hold multiple pairs securely in foam inserts ideal for B2B distribution requiring mixed SKUs in a single carton.
Custom printed boxes with die-cut inserts reinforce brand messaging on arrival. Corrugated cartons lined with honeycomb paper protect frames during transit and meet most carrier stacking requirements reducing puncture risk. Include silica gel packs to control moisture and anti-tarnish strips for metal frames. Mandatory labels for lens UV categories and batch codes should appear on each inner box and outer carton in clear durable print complying with GS1 barcode standards. This is where it gets interesting… integrating RFID tags into packaging enables real-time inventory tracking cut mis-shipments and provide clients immediate stock visibility.
Estimate packaging cost per unit by calculating box materials printing set-up and assembly labor. Negotiating with packaging suppliers on volumetric discounts often lowers unit rates significantly above threshold volumes. Bulk orders destined for multiple markets may require labeling variations for language and regulatory marks adding complexity and cost. Ready for the good part? modular packaging designs that use standardized box sizes with interchangeable inserts support flexible SKU combinations while keeping tooling costs for custom inserts manageable.
Well-designed packaging not only secures product integrity but serves as a touchpoint reinforcing brand quality and fostering unboxing experiences that delight end-users and strengthen B2B relationships.
Packaging Type | Key Features | Cost Considerations |
---|---|---|
Hard Case | Durable ABS metal-reinforced premium look | Higher material and shipping weight |
Soft Pouch | Lightweight scratch protection | Lower cost limited structural support |
Corrugated Carton | Honeycomb lining high crush resistance | Moderate cost scalable volumes |
Custom Printed Box | Brand messaging inserts compartments | Set-up fees volume discount thresholds |
RFID-Enabled | Real-time tracking inventory visibility | Tag cost integration infrastructure |
13 How Do You Scale Production From Small To Large Batches?
Scaling production demands careful capacity planning process refinement and supply chain resilience to maintain quality while meeting growing volumes. But here’s the kicker… jumping from small runs to mass orders without verifying capacity often yields bottlenecks that derail delivery schedules. Begin scaling by mapping current cycle times across molding assembly inspection and packaging stations identifying process steps with least throughput headroom. Invest in parallel processing equipment or second-shift labor for these critical paths while monitoring yield metrics to catch emerging quality drift under higher loads.
Vendor relationships also require renegotiation. Raw material suppliers may set price breaks at higher volume tiers but demand longer lead times or larger minimum purchases. Align purchase orders with sales forecasts and safety stock levels to avoid stockouts without over-tying capital. This is where it gets interesting… implementing vendor-managed inventory programs transfers inventory carrying responsibilities to suppliers reducing capital tie-up and ensuring continuous supply.
Internal process automation like robotic polishing and automated vision QC projects further flatten scaling costs by reducing manual labor inputs per unit. Validate process capability indices (Cp Cpk) under new volume conditions ensuring tools and machines operate within tolerances at sustained cycle rates. Ready for the good part? achieving Six Sigma defect levels (3.4 DPMO) through SPC and Kaizen workshops shrinks rework rates enabling smooth ramp-ups from hundreds to tens of thousands of units per month.
Ultimately scaling production relies on blending capacity upgrades process automation and collaborative supply chain strategies to deliver consistent quality on time irrespective of order size empowering brands to seize market opportunities swiftly.
Scaling Element | Action | Impact |
---|---|---|
Capacity Analysis | Identify bottlenecks throughput mapping | Targeted equipment or labor investments |
Vendor Agreements | Volume discount safety stock alignment | Cost savings reduced stockouts |
Automation | Robotic polishing vision QC | Lower labor cost consistent quality |
Process Control | SPC capability index monitoring | Early defect detection maintain yield |
Continuous Improvement | Kaizen workshops Six Sigma initiatives | Rework rate reduction |
14 How Is Sustainability Integrated Into Production?
Integrating sustainability appeals to eco-conscious buyers reduces waste and can unlock premium pricing while aligning with global environmental standards. But here’s the kicker… sustainability isn’t just green marketing it demands lifecycle thinking across materials sourcing production and end-of-life disposal. Start with recycled acetate made from post-consumer plastic scraps filtered and reprocessed into sheet form. That approach closes the loop diverting waste from landfills yet requires thorough contamination screening to maintain color consistency and structural integrity. Metal frames benefit from recycled stainless steel or titanium sourced via certified smelters that track chain of custody ensuring conflict-free raw materials.
Manufacturing process adjustments also cut carbon footprint. Switching to LED-powered UV curing machines for lens coatings lowers energy consumption versus legacy mercury vapor lamps. Capturing and reusing process water in rinse cycles toward cleaning or coolant reclaims resources and reduces utility bills. Packaging choices extend sustainability: biodegradable pouches printed with water-based inks and boxes made of 100 percent recycled paper that comply with Forest Stewardship Council standards. This is where it gets interesting… offering take-back programs for end-of-life eyewear creates brand loyalty and drives material reclamation further closing loop economies.
Transparency through environmental product declarations EPDs and third-party certifications like Cradle to Cradle or ISO 14001 strengthens buyer trust. Publicizing carbon footprint metrics per unit and year-over-year improvements resonates with corporate procurement teams under ESG mandates. Ready for the good part? quantifying water and energy savings per pair of sunglasses in annual sustainability reports converts abstract claims into tangible business outcomes showcasing corporate responsibility.
By embedding recycled materials process efficiencies and closed-loop initiatives you reduce environmental impact cultivate brand differentiation and meet rising regulatory demands empowering B2B customers seeking responsible suppliers.
Sustainability Area | Initiative | Benefit |
---|---|---|
Recycled Acetate | Post-consumer plastic reclamation | Waste diversion premium product appeal |
LED UV Curing | Energy-efficient coating process | Lower electricity consumption |
Water Reuse | Rinse cycle capture reuse | Reduced utility costs |
Eco Packaging | Biodegradable pouches recycled boxes | Lower landfill contribution |
Take-Back Program | End-of-life collection material reclamation | Closed-loop economy enhanced loyalty |
15 How Do You Troubleshoot Common Production Issues?
Production hiccups span from frame warping lens scratches to hinge misalignments each demanding targeted remedies to restore output flow and product integrity. But here’s the kicker… rapid troubleshooting protocols minimize downtime preventing minor defects from cascading into major rejects. Frame warping under heat bending often indicates incorrect water bath temperature or uneven mold pressure. Adjust bath thermostats in 2 °C increments and inspect clamp force readings distributing even pressure across frame fronts and temples.
Lens scratches during cutting or insertion frequently stem from worn diamond-tipped tools or misaligned beveling guides. Establish tool replacement schedules based on cumulative cycle counts rather than visual wear alone. Re-calibrate guide rails monthly ensuring clamps hold lenses steady without slippage. Hinge misalignment or binding reveals hole drilling drift or torque mis-settings. Re-measure barrel hole spacing against CAD data using laser distance tools and reset torque drivers to factory calibration specs. This is where it gets interesting… introducing quick-release modular fixtures enables technicians to swap tooling plates in under two minutes slashing changeover delays during troubleshooting.
Quality data logs form the backbone of issue diagnosis. Tag defective units with time stamp operator ID shift code and defect type feeding that data into SPC software for root cause analysis. Trend charts spotlight recurring issues linked to specific molds or tools guiding maintenance schedules. Ready for the good part? cross-departmental rapid response teams convene weekly using fishbone diagrams and five-why sessions to identify systemic failures preventing repeat occurrences.
By implementing structured troubleshooting workflows tool maintenance protocols and data-driven root cause analysis you resolve production issues swiftly safeguard delivery timelines and maintain consistent product quality vital for B2B credibility.
Issue Type | Likely Cause | Corrective Action |
---|---|---|
Frame Warping | Uneven water bath temperature pressure | Adjust thermostat recalibrate clamps |
Lens Scratches | Worn cutting tools misaligned guides | Replace tools realign bevel fixtures |
Hinge Binding | Hole spacing drift torque mis-settings | Re-measure drill coordinates reset torque |
Adhesive Overflow | Excessive dispense volume curing error | Adjust dispenser volume UV timing |
Coating Defects | Vacuum sputter imbalance coating thickness | Rebalance target cathode cleaning |
Conclusion
Effective sunglasses manufacturing weaves together material expertise process engineering rigorous quality checks and strategic supplier partnerships. Following these fifteen steps gives brands a comprehensive roadmap from initial concept through sustainable production and issue resolution. Investing in precise cost estimation scalable tooling design and transparent compliance practices reduces risk and enhances client confidence. Armed with these insights you can streamline workflows accelerate time to market and uphold exceptional product standards that win long-term B2B trust.
FAQ
Q1: What is sunglasses manufacturing?
Sunglasses manufacturing encompasses material selection design prototyping tooling assembly quality control and regulatory compliance to produce frames and lenses that meet safety and style standards.
Q2: How does the prototyping process work?
Prototyping involves cutting raw blanks into frame shapes CNC machining refining edges by hand installing hinges fitting test lenses and iterating based on fit comfort and visual inspections until final approval.
Q3: What is minimum order quantity for custom sunglasses?
Custom sunglasses often require an MOQ of 200–300 pairs per model though stock programs may permit smaller sample orders to validate design and quality before scaling.
Q4: How long does a typical production run take?
Lead times for production runs vary by order size and complexity but generally span 30–45 days after prototype sign-off with expedited options available for rush projects.
Q5: How can I ensure consistent quality across batches?
Implement multi-stage QC gates incoming material checks inline mold verifications automated vision inspections and final batch audits supported by SPC analysis to maintain uniform standards.